Powder metallurgy (PM) offers some tremendous advantages in the manufacturing of titanium suppressors. In particular, titanium powder metallurgy (PMTi) offers the best mix of strength, temperature stability, and affordability. Let’s take a look at the challenges surrounding suppressor manufacturing, how titanium compares to other materials, and why PMTi has a competitive edge.
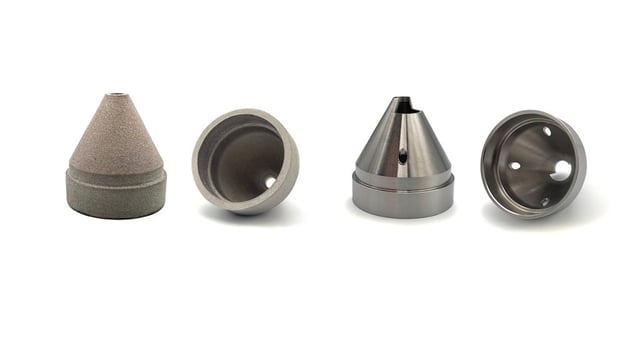
Challenges in Suppressor Manufacturing
A firearm suppressor, sometimes called a ‘silencer,’ is designed to reduce the noise from firing a gun. Unlike in popular movies, a suppressor does not make the gun silent; it merely reduces the noise to below dangerous levels. The suppressor will reduce the speed of the burning gases as they pass from the barrel and into open space.One of the biggest challenges with suppressors is the cost. In the United States, suppressors require a $200 tax stamp and paperwork, in addition to the cost of the suppressor itself, which is complex and expensive to manufacture. Therefore, suppressors need to have a long life. A way to extend the life span is the ability to remove, replace, and clean the baffles inside the suppressor.
Another big challenge with suppressors is fighting corrosion and dirt. In a normal firearm, particles from the primer, debris from the burning powder, and small bits of lead and copper from the bullet are expelled from the barrel when the gun is fired. The purpose of the suppressor, however, is to slow down all these particles, as well as the hot gases, meaning much of this contamination gets trapped in the suppressor. Therefore, the suppressor body and the baffles must be resistant to corrosion from any chemical contaminants.
The suppressor must also be strong and resistant to wear and erosion. The presence of hard particles and the high temperature of the gases can quickly erode the baffles as the bullet passes through.
Another challenge of suppressors is that they can get quite hot during sustained rapid fire, such as might be encountered with an automatic weapon. As materials heat up, they typically lose their strength. Deformation of a material at elevated temperature is called creep, and the ability to retain strength at elevated temperature is called creep resistance. This is typically evaluated by measuring the elongation of a tensile sample at an elevated temperature and under a constant pressure.
Common Suppressor Materials
Suppressors are typically made from a few alloy families. Stainless steel, nickel base alloys, aluminum, and titanium alloys are commonly used, and there are advantages and disadvantages to each alloy family.Stainless Steel
Stainless steel alloys are strong, tough, and corrosion resistant. The corrosion resistance allows for harsh weather conditions on the outside and reduces the effects of fouling internally. The high temperature durability of the stainless steel allows for some rapid-fire situations. Stainless steel suppressors are relatively heavy, stainless steel being the second most dense of the common suppressor materials.Aluminum
Aluminum alloys are lightweight and inexpensive. Their low density is useful for reducing weight when it is necessary to carry a suppressed firearm for long distances. But they also have a lower melting temperature and tend to heat quickly during rapid-fire situations.Most importantly, the aluminum does not have to melt to be an issue, as many aluminum alloys lose most of their strength at only half their melting temperature. A common aircraft aluminum alloy, 6061-T6, sees a yield stress reduction from 276 MPa to 12 MPa when the temperature increases from room temperature to 370 C. Heat is often the limiting factor in suppressor designs, but it is a significant limitation when using aluminum as the construction material. Aluminum alloys have low creep resistance.
Titanium
Titanium alloys are strong, tough, and corrosion resistant. While titanium alloys are more expensive than the previous two alloy families, they combine some of the desirable properties of each; they are strong yet low density. They have good thermal stability and corrosion resistance, without significantly adding to the overall weight of the system.One of the more useful titanium alloys is Ti-6Al-4V, which is used for its high strength to weight (or strength to density) ratio, its excellent corrosion resistance, and relatively high tensile properties combined with robust ductility. Of the various titanium alloys, Ti-6Al-4V is currently the most popular alloy in medical, aerospace and suppressor applications.
PM titanium processing techniques can provide substantial improvements to the Ti-6AL-4V alloy; by precisely controlling the oxygen content the creep resistance can be improved by an order of magnitude.
There are specialty titanium alloys that can provide substantially higher creep resistance, basically eliminating deformation below 450 C (842 F). The most popular creep resistant alloy is Ti-6Al-2Sn-4Zr-2Mo, however this alloy has not found great use in the suppressor field because of the elevated cost of wrought or casting stock material. This material can be successfully processed using PM techniques at costs similar to the popular Ti-6Al-4V alloy, opening up new opportunities for economical, higher performance titanium suppressor components.
Nickel Base Alloys
Nickel base alloys are a popular choice for their combined corrosion resistance and high temperature strength. These alloys are commonly used in the high temperature section of jet engines and other turbine applications. They have the best high temperature performance of the materials commonly used for suppressors. Nickel base alloys are commonly used on suppressors that will be subjected to sustained rapid fire. They are also the densest of the popular suppressor materials, resulting on a heavier product.Commonly used materials come from the Inconel and Stellite families of alloys. These alloys are often very expensive, as it must be cast under vacuum or a blanket of inert gas. These alloys have added cobalt and sometimes chromium for corrosion resistance.
Comparison Chart of Alloy Options for Suppressors
A table comparing physical properties of different alloys is shown below. The most desirable properties are highlighted.Material | 17.4 PH Stainless Steel | 6061-T6 Aluminum | Ti-6Al-4V Titanium | Inconel 625 Nickel-base |
---|---|---|---|---|
Yield Strength (MPa) | 1070 | 276 | 880 | 1050 |
Density (g/cm^3) | 7.80 | 2.70 | 4.43 | 8.44 |
Strength to Weight (MPa *cm^3/g) | 101 | 102 | 198 | 12 |
Hardness | 29 HRC | 60 HRB | 36 HRC | 98 HRB |
Source: http://www.matweb.com
Ti-6Al-4V shows the best combination of mechanical properties as compared to other common alloys. The higher density as compared to aluminum is quickly countered by the higher strength to weight ratio, as well as by the fact that the strength quickly decreases with higher temperature in the aluminum alloys. The hardness is used as a proxy quantity to characterize wear and erosion resistance; the harder the substance, the slower it wears.
While the nickel alloys, such as Inconel 625, show the best high-temperature performance, the added weight is a major disadvantage to hunters, who are looking for something lightweight to carry in the woods. Law enforcement and military applications often call for lightweight materials as well. Because the titanium alloy’s high-temperature performance is adequate for most applications, and the cost and weight are lower, titanium alloys are a good choice for suppressor material.
Powder Metallurgy: Reduced Costs
Ti-6Al-4V is a great choice for manufacturing suppressors, but that is only part of the story. To physically manufacture the suppressors, PMTi offers an economic way to create complex geometries and reduce the overall cost as compared to other manufacturing methods.
Proper, careful mold design can lead to cost savings for mass production of suppressor bodies and baffles. While there is a nominal upfront cost for tooling, that cost is easily offset by the lower part cost. Tooling cost for PM titanium are substantially lower that the cost for investment casting or metal injection molding and can often be incorporated in the part pricing. Furthermore, the precision of the PMTi process produces near-net-shape parts, leading to very little waste, reduced post post-process machining, and other expensive processing found in techniques such as investment casting or machining.
Powder Metallurgy: Increased Performance
Perhaps the greatest advantage to the PMTi process is the potential for improved suppressor performance. PMTi offers lightweight, strong, corrosion resistant alloys available in a near-net shape. Furthermore, PMTi can precisely control the oxygen content, increasing the creep resistance for high temperatures during rapid fire situations.
Powder metallurgy also allows for near-net shape design. The molds are designed to reduce the amount of machining required on each piece, ultimately bringing down the cost and lead time for high-volume production.
The final geometry is machined in each suppressor, which can be based on acoustics modeling of the gunshot. Baffles can be shaped to muffle sounds much more efficiently than many other traditional manufacturing techniques would allow. They can create tight-fitting metal-to-metal seals that allow the user to clean the suppressor and also reassemble it tightly to prevent escaping gases or excess vibrations.
The potential to create more efficient suppressors is available through PMTi. With the urban environment encroaching upon the “Great Outdoors,” such suppressors offer a method to reduce noise pollution in hunting areas and shooting ranges, as well as to protect the hearing of military, law enforcement, and sportspeople alike.
Reduce the Cost & Increase the Performance of Your Suppressors
Interested in learning more about PMTi-made suppressor parts and Praxis’ unique advantage, book a meeting with our CEO, Joe Grohowski.