Titanium Powder Metallurgy Suppressor Baffles
Lighter. Cheaper. Better!
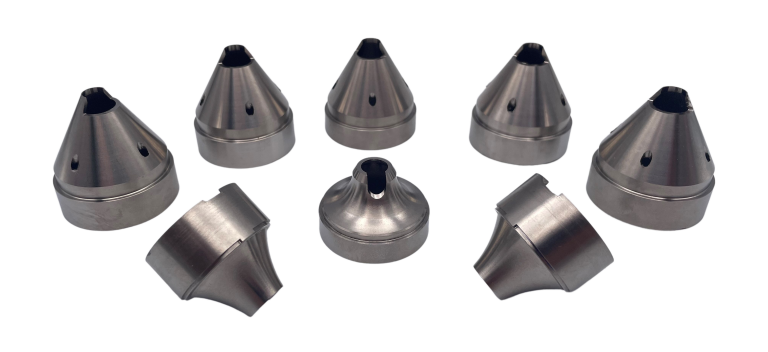
Suppressor Baffles
Material/Machine Use
Up to 80% Reduction in Raw Material Usage
Cost Savings
Typically, Over 30%
Material Performance
ASTM B988 Tensile Properties
Weldable
Laser or TIG weldable
Performance Advantage
Increased High-Temperature Properties
Mass Production Process
Tooling Required (starting at $5,000)
Minimum Monthly Volume = 500 parts per month
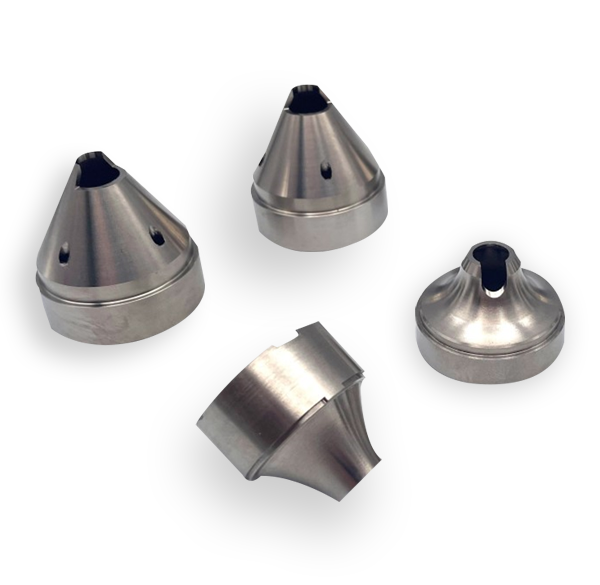
The Perfect PMTi Part
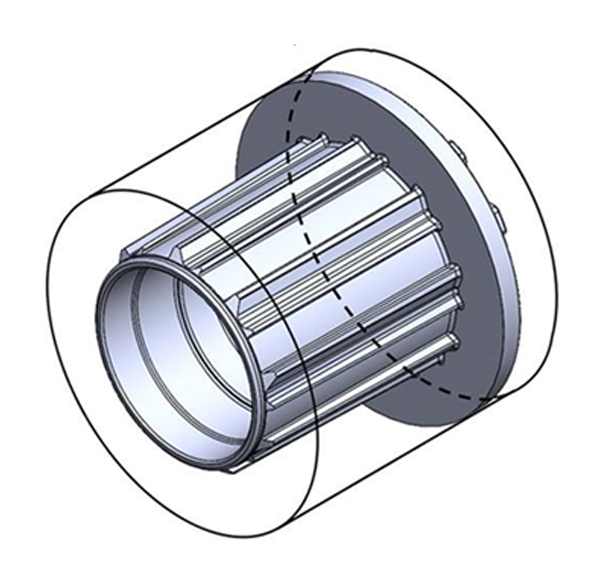
- Radial symmetry
- High Annual Volume (>10,000/year)
- Low Effective Density
- Baffles are an excellent application
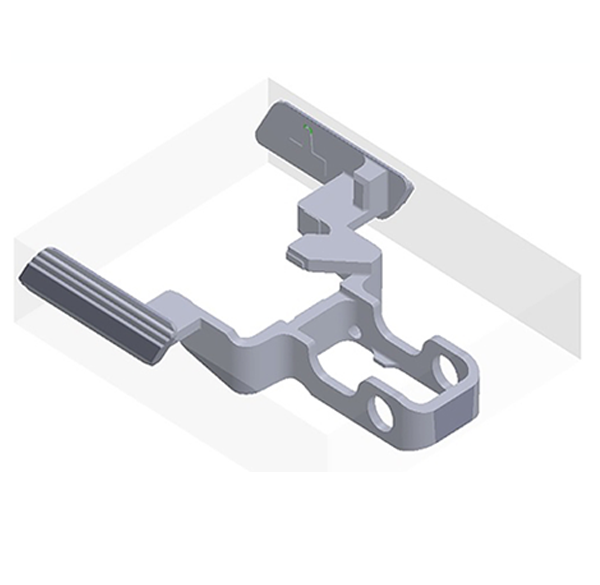
The Concept of “Effective Density”
The less material in the total “envelope” of the part, the more material cost savings are possible with powder mettallurgy.
In this example, the final part only occupies 6% of the total envelope part and weighs 5 g.
Transforming Titanium Baffle Manufacturing [Free Resources]
Unlock the potential of titanium suppressor baffles with insights from industry expert Joe Grohowski of Praxis Technology.
✅ Get access to our 25-minute webinar recording, plus get these free additional resources
📄 Titanium Suppressor Baffle Manufacturing Guide
📊 Cost and Timeline Optimization Checklist
🔬 Advanced Materials Comparison Chart
Economical Manufacturing of Suppressor Baffles
.png)
- Near net-shape fabrication reduces material costs
- Meets mechanical requirements of ASTM B988
- Product specific benefits for suppressor applications
Book a meeting with our CEO Joe Grohowski to learn more!
——— ABOUT
Praxis Technology
- Experts in Titanium Powder Metallurgy (PM)
- Leader in titanium baffle production via PM
- Manufacturing titanium implants via PM since 2008
- Tier 1 supplier to major OEMs
- 50+ medical implants in production
- >750,000 implants in service
Manufacturing Technologies
- Titanium MIM: Metal injection molding of small complex medical implants
- Porous Titanium: Patented bone ingrowth material duplicating bone porosity
- PMTi: Low-cost Compacted Ti-6Al-4V
- TiRx: Proprietary heat treatments for MIM and additively manufactured parts
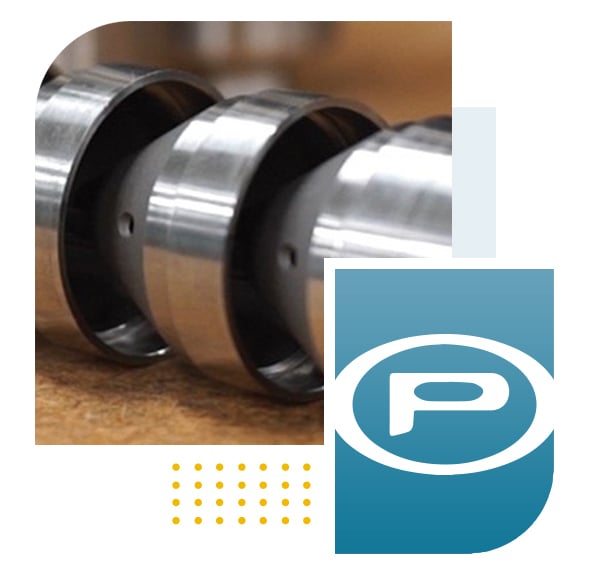
PMTi Production Timeline & Costs
Manufacturing Methods Comparison
PRAXIS PMTI-6AI-4V |
INVESTMENT CASTING |
CONVENTIONAL MACHINING |
|
Per part cost |
Low |
Low |
High |
Creep performance |
High |
Low |
Low |
Upfront Tooling cost |
Low |
High |
n/a |
Weldability |
Good |
Poor |
Good |
Net-shape surface |
Good |
Poor |
n/a |
PMTi - A Material Advantage for Suppressor Baffles
Slightly elevating the oxygen increases tensile properties via interstitial strengthening.
This strengthening mechanism is compositional rather than microstructural and persists at higher temperatures, delivering improved creep performance over conventionally formed titanium
Lamellar structure provides better creep strength than wrought or cast product.
Elevated oxygen also provides slight increase in hardness (~40HRC), which can improve wear resistance.
Tensile strengths compare favorably with ELI and NI Grades, elongation slightly less.
.png?width=768&height=612&name=COMPARISON-of-creep-graphic_FINAL_v2-768x612%20(1).png)
Material Compliance: PMTi Ti-6Al-4V
Praxis Typical PM values compare well with standard specifications
Standard PM material is best value for suppressor components
Heat treated PM material has exceptional performance
Praxis’ typical values surpass both the cast & wrought strength specifications
|
STANDARDS | SpotlightWP | ACTUAL (Typical) | Add New | |
ELEMENT/PROPERTY | ASTM F381 Ti-6AI-4V Wrought |
ASTM B367 Ti-6AI-4V Cast |
ASTM BP88 Ti-6AI-4V PM |
Praxis PM Ti-6AI-4V Standard |
Praxis PM Ti-6AI-4V Standard |
MECHANICAL PERFORMANCE | 29+ | 4 | 1 | 33 | Add New |
UTS MPa (kis) | 895 (130) | 860 (125) | 985 (130) | 1070 (155) | 1138 (165) |
YS MPa (ksi) | 828 (120) | 758 (115) | 828 (120) | 945 (137) | 1034 (150) |
Elongation % | 10% | 8% | 10% | 12% | 16% |
Reduction of Area | 25% | 14% | 25% | 25% | 40% |
CHEMICAL REQUIREMENTS | Add New | Add New | Add New | Add New | CHEMICAL REQUIREMENTS |
Nitrogen | <0.05% | <0.05% | <0.05% | <0.03% | <0.03% |
Carbon | <0.08% | <0.10% | <0.08% | <0.02% | <0.02% |
Hydrogen | <0.0015% | <0.0015% | <0.0015% | <0.01% | <0.01% |
Iron | <0.40% | <0.30% | <0.40% | <0.20% | <0.20% |
Oxygen | <0.20% | <0.20% | <0.30% | <0.34% | <0.34% |
Aluminum | 5.5-6.5% | 5.5-6.75% | 5.5-6.75% | 5.5-6.75% | 5.5-6.75% |
Vanadium | 3.5-4.5% | 5.5-6.75% | 5.5-6.75% | 5.5-6.75% | 5.5-6.75% |
Titanium | Balance | Balance | Balance | Balance | Balance |
Metallographic Comparison
Wrought Ti-6AL-4V
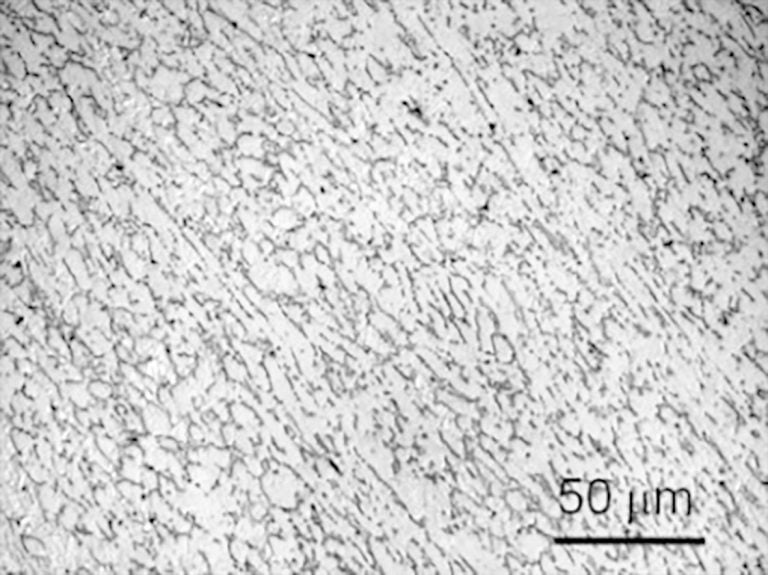
- Fine grains
- Directionality from working
- Many microstructures possible based on thermal & mechanical history
PMTi Ti-6Al-4V – HIP’ed
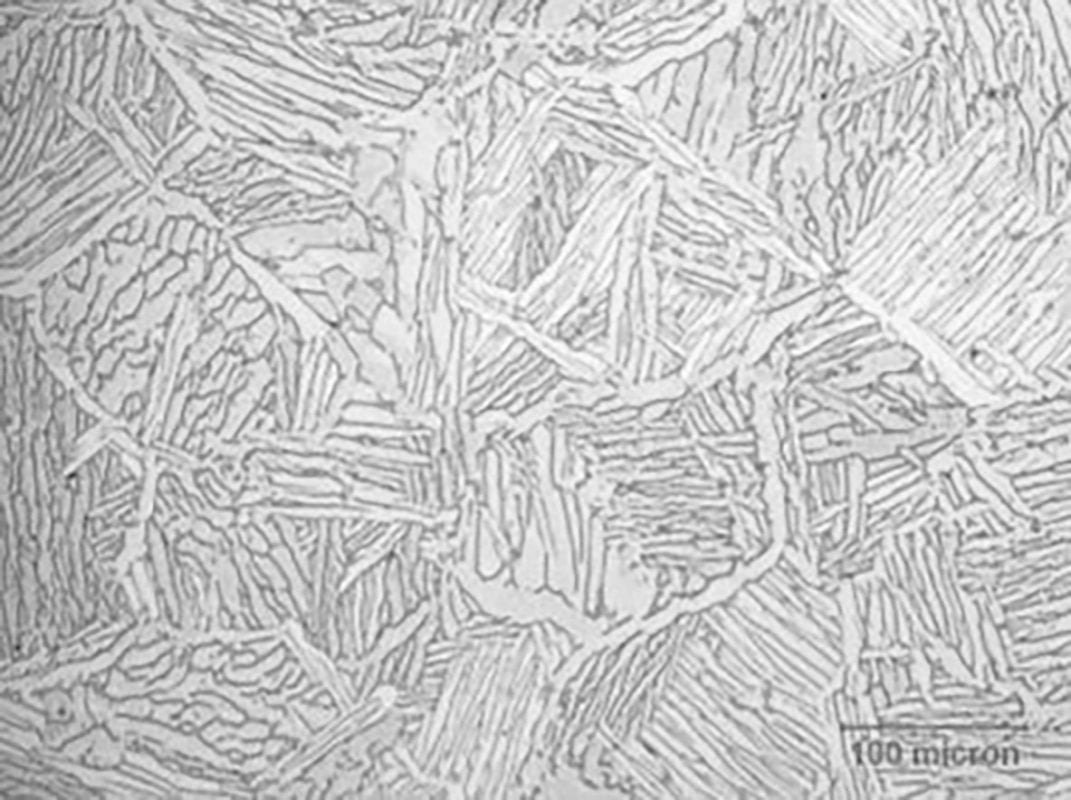
- Coarser grains
- Coarse lamellar structure
- Alpha colonies with grain boundary alpha of similar size
- Intergranular beta
HIP’ed to Achieve Full Density
As-sintered
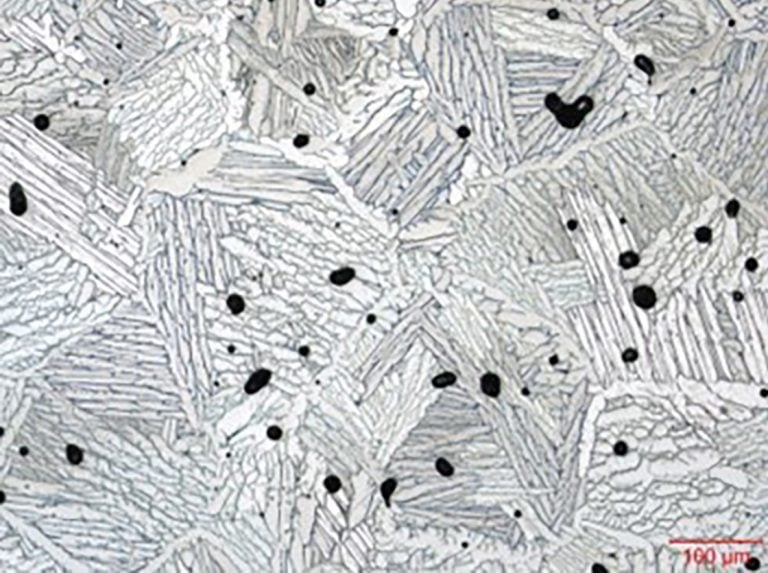
As-Sintered >96% Dense
Hot Isostatically Pressed
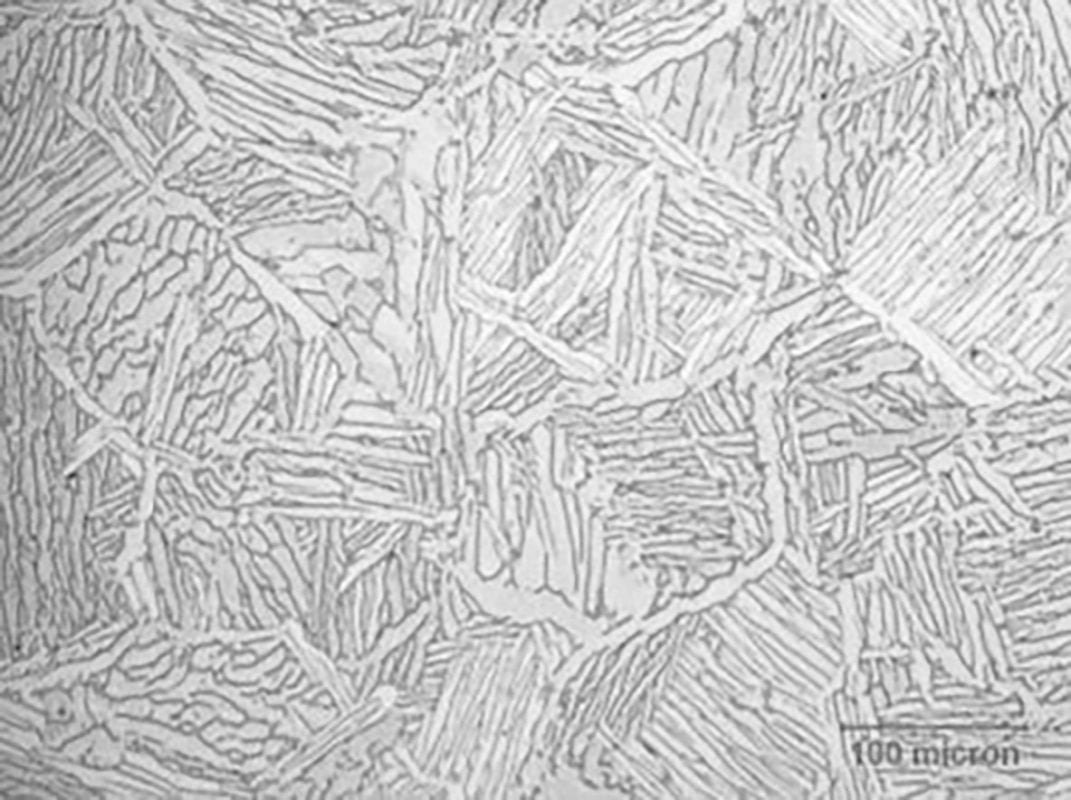
100% Dense
Market Focus
Leaders in Highly Regulated & Performance Critical Markets
Defense
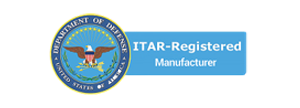
- FFL
- ITAR Registered
Aerospace
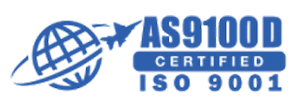
- AS9100D
- ISO 9001 Certified
Medical Device
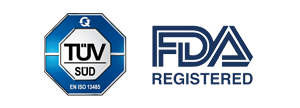
- ISO 13485 Certified: Production
- FDA Registered
- CFR 21 Part 11 Compliant
- FDA Master File
- Product certified to ASTM F2885-17